Another good rule of thumb is to keep your arc length similar to the diameter of the electrode you are using. There may be times where a length is given on a part and the location of the weld will be given with a dimension in order to achieve the correct location.
What Are The Basic Welding Symbols Welding Welding Projects Welding Table
A cnom t anom2 anom1 a a nom nom nom a partially penetrated butt weld b T joint Figure 38 Effective width For T joints full penetration is assumed in the case of anom1 anom2 t 5 t cnom 319 cnom 3 mm.
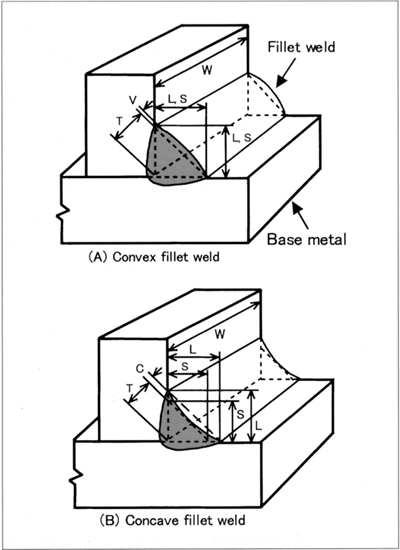
In welding fillet the normal arc length is. If the plates are different thicknesses the thinner plate thickness should be used. Information below the reference line refers to the arrow side of the weld. I remember one particular job in the aerospace world where an 012 patch was welded to 020 15-7ph stainless.
It can be as small or as large as the design requires or the welder thinks fit but there are limits on the size for other reasons. Stringers are beads layed with no weave. Arc length faults can share many similarities with.
While the arc distance can fluctuate depending on a lot of factors the base is taken to be around 010 inches. Also check out this article about slag in welding. This is difficult to measure so tends to be estimated as 07 x leg length for a flat profile mitre fillet as in the photo.
246 Intermittent Fillet Welds Minimum Length. The fillet weld is the cheapest type of arc welded joint since all that has to be done is to stand one piece of metal against another and run a welding rod or gun where the metals touch. Of undercut depth for 2 in.
A normal arc length is considered equivalent to the. Other things that make a big difference in tig welding Electrode angle also makes a difference. The effective length of a fillet weld might be taken as the total size of the full-size fillet much less one leg length s for every end which does not continue around an edge.
Deep for ¾ in. Ideally the weld should be 05-1mm clear of the top corner. This shows a 6 fillet weld to be applied to the arrow side.
Weld is part of a 3-on-6 intermittent fillet weld. A fillet weld with an efficient size much less than 4s or much less than 40 mm must not be utilized to carry load. The weld size is not defined by the thickness of the parts being joined as in the case of the butt weld.
Weld has undercut and the undercut is 116 in. In general the arc length is 010 inch and this measurement is taken as a base. Partially penetrated butt welds may be designed as fillet weld with an effective width of a anom 2 mm see Figure 38a.
The weld length will be provided on the right side of the fillet weld symbol. Typical arc voltages in SMAW are in 50-100 volts. An example t-joint is shown below with a weld size of 38 on 12.
One half of the weld penetration is combined with the base measurement and this results in the arc length for a certain amperage. That job required a super tight arc along with 020 electrodes. With the conventional arc welding processes it is difficult to deposit a fillet weld with a throat less than some 2mm.
GMAW uses a consumable electrode. To do this we employ basic algebra. The minimum length of an intermittent fillet weld shall be 1-12 in.
To get the throat size for an equal-leg fillet weld simply multiple the leg size w by the cosine of 45 which is 0707. To compensate for this reduction in throat thickness it may be necessary to specify a deep penetration fillet weld. This is in addition to the possibility of the lack of fusioncold cracking mentioned above due to the rapid cooling rates experienced by small fillet welds.
Arc length is the distance from the tip of the electron to the work. 247 Fillet Weld Terminations 2471 Drawings. This is why leg sizes are called out for fillet welds.
As with flat joints multiple stringers are used to increase the material in the weld for plate thicker than about 6mm. Increasing arc length will increase the voltage. Fillet weld for the full length of the plate.
Hatching lines may be used to indicate the length of a weld instead of using a dimension on the weld symbol itself. Weld and it has 116 in. Arc welding is a constant current process but the arc length has an effect on voltage.
The designer may therefore specify a slightly smaller leg length compared to the thickness of the component. So a 0330 leg would yield a 0330 x 0707 0233 throat. Reducing the arc length will decrease the voltage and this reduces the heat in the weld.
Diameter of the core wire in the electrode What arc length gives the best blend into the edges of a weld bead. Imagine if three of those fall within 12 in. Youve got a 3-in.
The length and disposition of welds including end returns or boxing shall be indicated on the design and detail drawings. A 45 degree angle is commonly used for welding a fillet weld.
Welding References Education Center Kobelco Kobe Steel Ltd
The Abc S Of Arc Welding Education Center Kobelco Kobe Steel Ltd
The Abc S Of Arc Welding Education Center Kobelco Kobe Steel Ltd
Read These Information And Tips Here Metalworkingideas Welding Projects Metal Welding Mig Welding
Welding References Education Center Kobelco Kobe Steel Ltd
Arc Welding Faults Examples Of Speed Arc Length And Current Problems Welding Projects Welding Types Of Welding
Welding References Education Center Kobelco Kobe Steel Ltd
0 comments:
Post a Comment