It must be check by welding inspection company. Extrusion is a continuous high production volume process.
Solved Projection Welding Can Be Considered As A Mass Production Form Of Self Study 365
Carbon steel iron cast steel cast iron.
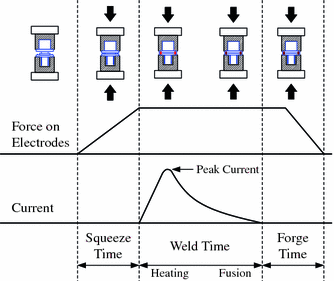
Projection welding can be regarded as a mass production form of. A WPS is a written document that provides direction to the welder or welding operator for making production weld in accordance code requirement. Arc welding resistance spot welding oxyfuel gas welding. However the only difference is in butt welding.
One of the main differences between conventional sheet-to-sheet resistance welding and projection welding is that projection welding is a dynamic process involving considerable movement of the upper electrode. It uses the same equipment as spot welding. The heat generated creates a plastic state and produces fusion at the interface surfaces.
The metals having good weldability in descending order are. How does it work. Advantages of the extrusion process.
Some of the advantages of resistance welding are as under. MIG welding process is becoming increasingly popular in welding industry because of - a Its easy operation b Its high metal deposition rate c Its low initial cost d Both its easy operation and its high metal deposition rate 6. 5 and 6 it is possible to produce in a most surprising manner qualitatively extremely upright randomly reproducible weld connections according to the micrograph of FIG.
It can be regarded as a mass-production form of spot welding. Precision control in rapid mass production. The automobile industry uses projection welding to a very large extent.
Examples of fusion welding. The projection welding is particularly employed for mass production work ie welding of refrigerators condensers crossed wire welding refrigerator racks grills etc. A weld bead of wineglass design is produced in welding a plasma arc b electron from EG 123 at Cairo Higher Institute for Engineering Computer Science Management In.
Makes the weld air tight. The electrodes used are of disc or roller shape. The various types of resistance welding processes may be divided into the following four main groups.
Projection welding involves heating the area as it collapses under pressure. Con created with nitro PDF professi. This process can be used for both brittle and ductile materials.
All of the above. ME 383 Welding Processes. Makes the weld water tight.
Good mechanical properties and surface finish obtained. MIG welding process is becoming increasingly popular in welding industry mainly because of. Projection welding can be regarded as a mass production form of welding.
This welding process is also used for the fan covers and hollow metal doors. The costs of resistance welding are low while the quality of the welded part is excellent. It has many applications such as.
Welding heavier materials that cant be spot welded. The PQR documents what occurred during welding the test coupon and the result of. Iv Butt welding Butt welding is similar to the spot welding.
However in this process large-diameter flat electrodes also called platens are used. Cast iron iron carbon steel cast steel. Coalescence is accomplished by melting the two parts to be joined in some cases adding filler metal to the joint.
The softened metal is squeezed out to form a flash and a forged structure is formed in the joint. With the described construction of the projections in the forms shown in FIGS. Projection welding is mostly used for mass production.
Cross wire welding is a type of projection welding that offers advantages such as. 3 and 4 together with a course of the welding current and electrode force as shown in FIGS. Uses an external heat source and is probably the simplest of the mass production techniques used to join plastics.
Lower electrode efficiency and maintenance. Lower cost per parts manufacturing. It can easily create complex shapes too.
This process working operation is easy and flexible. Although Resistance Welding is now over 120 years old the joining of metals by the application of heat and pressure is much older. Technically it is a cross between spot welding and butt welding.
Projection welding RPW. Iron carbon steel cast steel cast iron. For this reason it is widely used on automobiles home appliances and general machine parts.
Cast steel iron carbon steel cast iron. Furthermore as the welding process is simple with fast production speed it is an important process in the sector where mass production is needed such as the production of automobiles. Projection welding can be considered as a mass production form of_____.
I spot welding ii seam welding iii Projection welding and iv butt welding which could be further subdivided into flash welding upset welding and stud welding etc. Welding it is necessary only to clamp them together under pressure and pass through them an electric current for a specific time. Projection welding is a type of resistance welding that focuses current and force to a single point or line at the beginning of a weld.
If desired the flash can be removed by subsequent machinery.
What Is Projection Welding Working Principle Advantages Disadvantages And Application The Welding Master
Process Parameters In Resistance Projection Welding For Optical Transmission Device Package Springerlink
Resistance Projection Welding 2018 04 05 Assembly Magazine
Process Parameters In Resistance Projection Welding For Optical Transmission Device Package Springerlink
Process Parameters In Resistance Projection Welding For Optical Transmission Device Package Springerlink
Practice Quiz On Electric Welding Welding Construction
Projection Welding An Overview Sciencedirect Topics
0 comments:
Post a Comment