Repair to the Horn Repair to the horn of a wrought iron base anvil can be accomplished with 6010 welding rod as needed. Cast iron is difficult but not impossible to weld.
Single Horn Anvil Cast Iron Anvil Blacksmith For Sale Forge Tools And Equipment Tool Parts Aliexpress
You also get rare in big sizesolder forged steel ones and forged steel ones with a steel top.
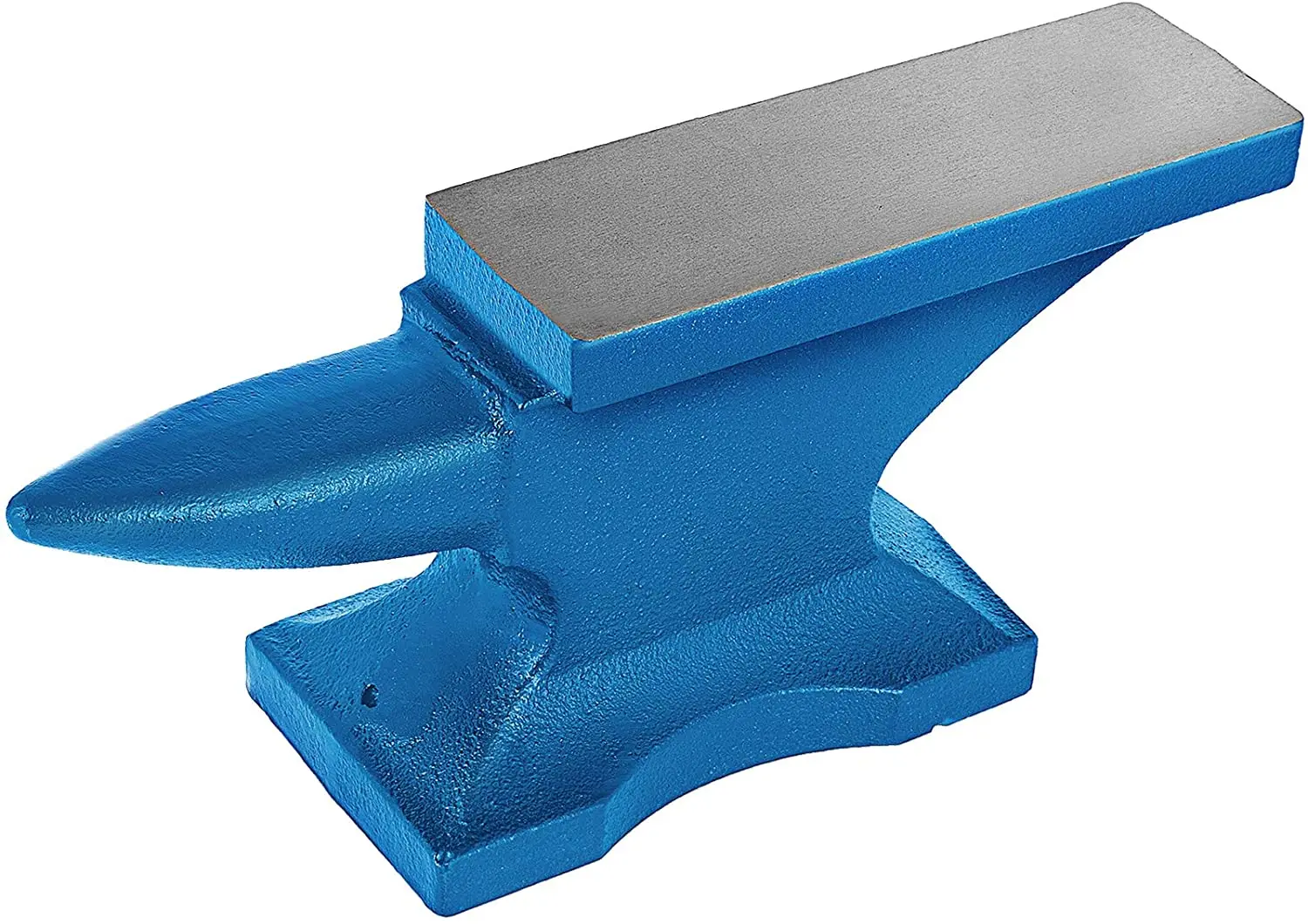
Welding cast iron anvil. By TamJeff Sat May 03 2014 1029 pm Perhaps weld some floating mild steel adapters to the A2 first and then weld those to the anvil. Unless it has a welded steel plate on top of the anvil cast iron is considered as the worst material for making the anvil. The repairs may be made in the foundry where the castings are produced or may be made to repair casting.
I strongly suggest you go with what Rob uses. Then grind the top smooth. Yes- anvil faces can be restored.
You might be able to braze the cast iron to the steel. Now clamp the plate on and make sure its where you want it. This worked but the anvil was still dead.
In MIG welding the electrode wires are usually nickel or Monel but copper alloys may be used. Welding the Plate On. The anvil has to be fixtured to hold it since its base is rough cast or rough forged.
Welding just a plate on my concern was how little fusion was happening between the two metals. Then weld all the way around the plate twice for extra strength. Flux cored wires nickel-iron and nickel-iron-manganese wires are also available for welding cast irons.
Then cut and grind the plate till it matches the anvil then shine up the face and the steel plate. Anvils made of cast iron with welded steel on top of it are considered much higher-quality anvils. Cast steel anvils repair well using the combination of the Stoody 2110 and the Stoody 1105 last three passes.
Use short beads of 1 12 move 6 around and keep going until finished. In the old days these anvils were made by forge welding a big hunk of several hundred pounds of wrought iron to a steel plate for the top. I know some early cast iron anvils had steel plates welded to the top but they would heat the top of the anvil in a forge or something for a while then basically power hammer it on to create a forge weld.
In both of these and the few other steel-faced cast iron anvils the sand mold is prepared in as many flasks as needed for the size of the anvil. Most hardfacing rod is NOT a good match for an anvil face. Welding on an anvil properly is something of an art to do it right without a damaging the tool-steel high-carbon face or b ending up with a disaster because you didnt pre- and post-heat properly.
Then fill in the holes with the welder a little above flush. Welding A-2 tool steel to cast iron. Note that if the body is cast iron and not cast steel you didnt say and both have been used there is a bit more of a risk but even more of a need for a good hard face.
A friend has a couple of 200lb Fishers steel faced cast iron anvils. Or a full cast steel in poor condition is probably the easiest to re-grind to a flat top. Preheat the anvil and run a stringer bead focused mainly on the anvil with a nickel 99 rod.
My dad has done both and if youve got the forge welded type go straight in with the 7018 but try not to get too much diffusion of the base metals like if you was welding hardfacing. For general use a cast one with a steel top is ideal if its in decent condition. Many anvils had have their face welded on.
The cast iron will melt at welding temperatures. I also have a new-ish 220lb Refflinghaus cast steel anvil. Follow that with either a 7018 or 309 stainless rod focusing the bead twards the steel plate.
In most cases welding on cast iron involves repairs to castings not joining casting to other members. Now depending on the age of the anvil it will be solid cast or cast with a forgewelded piece of harder steel on the face. Cast iron anvils are usually no heavier than 50 pounds.
That would make a fairly durable join. All cast iron All cast steel Cast iron with a steel top And cast steel with a steel top. I used to have a 143lb Peter Wright forged wrought iron with a steel face.
It is somewhat softer than the Columbian but is still one heck of an anvil. They are usually too hard for cutting with a flycutter. Dissimilar then hard facing or 7018.
Youll need a place you can build a substantial fire one large enough to bring that ASO to near orange heat. The technology used to do this was definitely not shade tree- it was a very sophisticated process evolved over 300 to 500 years and it involved the late 19th century version of a factory. What some smiths have done is to have the face Blanchard Ground a rotary surface grinder is used.
It was a great anvil but was getting a bit swaybacked. It takes a while to heat a 200 hunk of iron and steel to 400 or 500 evenly. However there is a variation of quality even.
You might arc weld around the edge but that would probably crack and spall the cast iron also. They did it by preheating the tool-steel face to welding temperatures and casting the molten cast iron steel in the rest of the mold. Star Badger Fisher and Vulcan are some of the names making these types of anvils.
Lay sticks of fluxed silver solder across the anvil about 34 apart and wire the plate. You cant forge weld cast to steel. I cant really do that.
Powders are based on nickel with additions of iron chromium and cobalt to give a range of hardnesses. This was usually a shallow flask for the face topped by a deeper flask for the body to the waist topped by a.
Amazon Com Flyhero 11kg Rugged Cast Iron Anvil Blacksmith Anvil Forge Anvil Portable Welding Tool Garden Outdoor
Rugged Cast Iron Anvil Medium Matthys
Rugged Cast Iron Anvil Medium Matthys
Rugged Cast Iron Anvil Small Matthys
Publicity Anvil Angele Small Anvils Anvils Forging Angele Shop
Jual Peralatan Rumah Tangga Portable Rugged Cast Iron Anvil Blacksmith Jakarta Barat Wiji Agustia Shop Tokopedia
9 Lb Cast Iron Anvil Anvil 009 Hand Tool Sets Amazon Com
Buy Olympia Tools 100 Pound Cast Iron Anvil 38 785 Online In Indonesia B073654fwh
0 comments:
Post a Comment