Gases become trapped in the weld. Cutting brass and in gunmetal LG1 LG2 causes porosity and fume problems with gas shielded arc welding.
Pdf Welding Problems With Thin Brass Plates And Tungsten Inert Gas Pulse Welding
They are also called Copper-Zinc alloys.
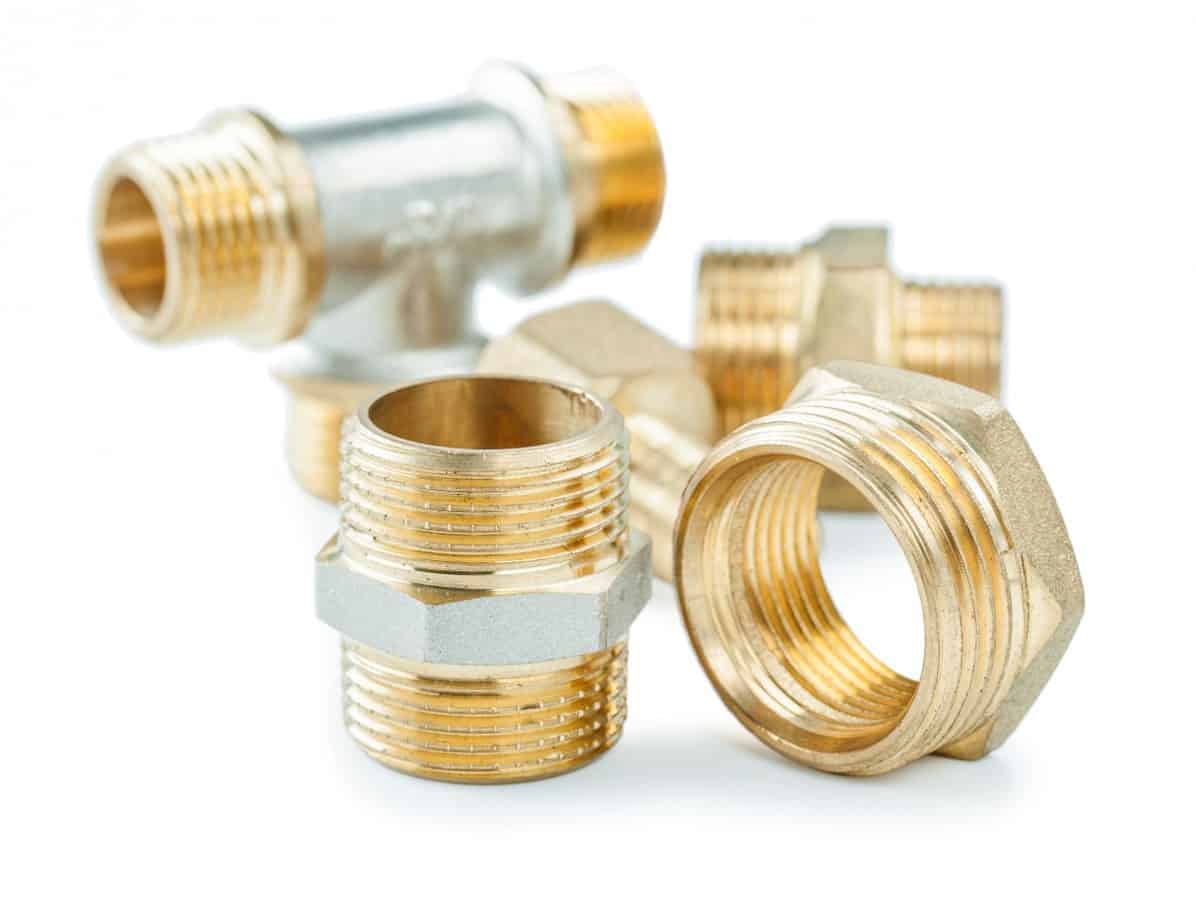
Welding brass porosity. Welds should be made using either silicon bronze Cu-Si-Mn or aluminium bronze Cu-AlFeNi consumables. Aluminum bronze alloys have a strong aluminium oxide film that forms on their surface. TIG welding process can be used to weld a wide range of metals like stainless steel chromium aluminum nickel alloys magnesium copper brass bronze and even gold.
Even then it still is sometimes there. If you are just starting out with brass welding it is advised not to go ahead with gas welding or oxy acetylene as the zinc component of brass tends to vaporize due to high heat. Using a longer arc may also increase its chances.
You will want to set it with 30-second pulses per second. It occurs when the electrode is not coated properly. Gas welding of brass is not recommended as the zinc will tend to vaporise causing fumes zinc oxide and porosity.
Zinc vaporization affect brass weldability can results in porosity and lack of fusion. The only way we can seem to keep it from happening is to hold the torch really far away and just barely melt the brass. Reduce the risk of porosity in brasses by using a zinc-free filler.
Due to brasss high conductivity it is recommended to use as little heat as needed to effectively create a weld pool. I tried searching but nothing has helped me so far. Some of the reasons that the cavities occur are.
Even though it flows out like it should and does not ball up it has the porosity. The main problem with welding the alloys is weld metal porosity caused by the zinc boiling off during melting. Now Ive been tig welding for about two years now 90 of my welding has been stainless and stainless to mild steel basically everything from 18g to 12.
On top of the fact that brazing basically involves less heat directed at the brass than welding will there are also fewer health risks to doing so. Brazing Vs Welding Brass A lot of people would argue that it would be far better to simply braze brass than to weld and in all honestly this is the right attitude more often than not. BRASS Brass is a generic term covering a wide range of copper alloys containing additions of zinc.
Porous Tig welds. All porosity is the result of bubble formation and all bubbles follow a basic relationship. Porosity in the condition in which the gas or small bubbles gets trapped in the welded zone.
Brass or Bronze 8800 117 202 157 062 Because the entrapped air will react with the molten metal the pore size will actually become smaller as the oxygen in the air. When you are using gas shielded arc welding and you add lead for free cutting brass and gunmetal it can result in porosity and fume problems. Brass is an alloy of Copper Zinc.
Additionally higher welding speeds reduces pore size in the weld. However PB2 phosphor bronze can be joined with. It seems like if we get the brass too hot it starts bubbling.
Phosphor Bronze coppertin alloys such as PB2 can be readily brazed or welded. Hey Guys Im new to the forum and not so new to welding. The most cited advantage of TIG welding is its excellent control over lower amperage rating like 10-200 amps which allows the welder to work on a thin piece of metal.
With the exception of brasses containing lead Pb all the brasses are weldable the low zinc alloys being the easiest. Filler metals for MIG or TIG welding brasses should not contain zinc. Porosity with MIG Welding.
This film gives them strong corrosion resistance. Zinc Oxide is formed in the process which causes porosity in the weld. This is because the zinc tends to vaporise in the arc leading to zinc loss and porosity in the weld.
Most liquid materials can hold a large amount of dissolved gas which evolves in the form of bubbles upon solidification. When it comes to MIG welding it is tiny gaps within the weld that weaken it and prevent proper weld adherence. To avoid porosity at the end of a weld be sure to allow the metal to cool off under your gas shield as exposure to the atmosphere can ruin the quality of the weld.
Zinc fuming is a critical issue when welding brass as zinc vaporizes when brass is melted during welding. The issue is concerning when welding high zinc based brass alloys. I have not had a single problem what so.
Some do no recommended gas welding brass since the zinc tends to vaporize and cause fumes and porosity. B Gas Porosity Gas porosity is the formation of bubbles within casting after it has cooled. All brasses which includes Gilding Metal can be silver soldered MIG and TIG However the addition of lead for free cutting brass and in gunmetal LG1 LG2 causes porosity and fume problems with gas shielded arc welding.
Either a silicon bronze or an aluminum bronze filler is best suited with brasses. It is caused by improper welding techniques. Porosity is the occurrence of an unwanted void or cavities in the weld material.
These flaws appear on the surface of the casting as pores which reduce the strength of the metal in that vicinity.
How To Weld Brass Welding Headquarters
Cu Ni Welding Part 3 Cracking Porosity In Cu Ni Welding General Technical Knowledge
How Can We Differentiate Pinhole And Porosity In Welding Quora
17 Causes Of Porous Tig Welds And How To Prevent Them Welding Mastermind
Three Ways To Reduce Weld Porosity On Your Assembly Line
Porosity Defect In The Fillet Weld Metal Of The Stainless Steel Stock Photo Download Image Now Istock
How To Weld Brass Welding Headquarters
This Is How To Fix Porosity In Welding Welding Mastermind
0 comments:
Post a Comment