A simple mistake might put you in a tough spot. Rusted body panels need to be repaired.
How To Sheet Metal Repair Or Patch Easily Youtube Auto Body Work Auto Body Repair Car Repair Diy
After all so-called TIG welding for tungsten inert gas is also a metal-inert-gas welding process.
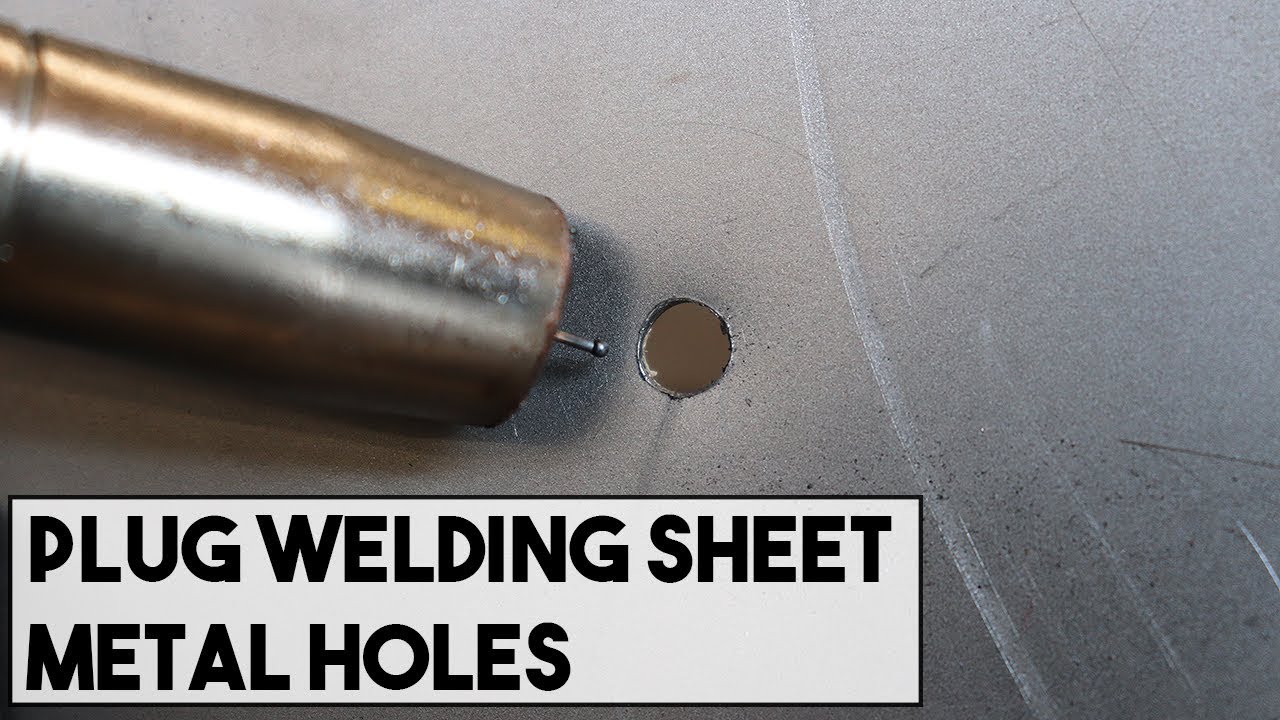
Welding sheet metal auto body. For thinner gauge sheet metal like 18 or 20 gauge we suggest 023 6mm wire in your MIG welder. Which Type of Welding. After having ensured the sheet metal has been properly cut and that the gaps are small enough for the metals to be joined there are a number of steps youll need to take in the process once you become an auto body technicianBe sure to use butt welding to ensure that seams dont overlap with one another and gently.
The Hobart mig welder comes with gas conversion. TIG welding sheet metal. It is better to use instead of a high percentage of CO2.
A 110 volt MIG welder can work perfectly for you. In this article we are taking a look at how people should go about welding sheet meta l what kind of wire and shielding gas need to be used along with some tips and tricks. Forget the larger 18-inch tungsten electrode and use a smaller one.
However welding is very crucial. MIG welding is the preferred method for most automotive bodywork and since sheet metal is the thinnest of metals a large expensive MIG unit is usually not required. Spot welding is usually used to join a panel of overlapping sheet metal parts that are usually 3mm thick.
The majority of the sheet metal welding Ive done was with a 90-amp 110-volt welder. First off never overlap seams always butt weld. If youre repairing an old car then youll almost certainly need to weld rusted sheet metal at some point.
Second never stitch weld youll warp the panels beyond repair. Since most body welds are made on sheet metal you do not need a high-performance welding machine. The ration of thickness should not exceed 31mm.
Its primary usage is in welding auto body and sheet metal. Read on to find out more. This article will provide you all the information that you will need to know before you start welding auto body sheet metal.
Otherwise you may find a lot more splatter than you have imagined. Its name derives from the term metal inert gas which is really a misnomer. Keep the Stick Out Short- Stickout of your MIG wire is important when welding any type of metal but especially sheet metal.
Holding the tip too far from the surface will cause the wire to have to come out too far to touch the metal. If you also want to use the MIG welder for DIY projects or heavier steel structures we recommend that you look at a MIG welder that operates at 230 volts. Dont attempt to weld thin materials like sheet metal with flux-cored wires which put more heat into the base metal.
Auto Body Training Students Should Learn the Steps to Sheet Metal Welding. When starting to learn auto body sheet metal welding with a MIG welder you should opt for a shielding gas that has a higher proportion of argon gas. When youre welding body panels you can either MIG weld.
Every restoration that passes through MCR needs some sort of sheet metal work that involves welding in new pieces so we thought we would show you how we join body panels together. Thus spot welding diameters go from 3mm to 125mm. This has become the most common type of repair and custom auto-body welding.
They can also cause costly future repairs if the rust spreads to vital components and damages them. When it comes to welding thin sheet metal like car body panels if you are not experienced and skilled enough then you can easily create a mess as blow holes in the sheet and make the metal useless. Actually 115 volt mig welders are often the best choice for welding sheet metal and a Hobart Handler 140 has all the features needed to weld thin sheet metal or even up to ¼ thick steel Get a gas conversion kit so you can run 023 bare wire.
Sheet metal is considered the most important part in automotive when it comes to doing work with metals. To weld sheet metal with solid wires use electrode positive EP or reverse polarity. It is better to avoid using a flux-cored wire when welding sheet metals.
Properly what is called MIG should be called according to the American Welding Society AWS GMAW for gas metal arc welding. This is because the strength of the joints depends on the number and size of the weld. Not only do they look horrible but they make the metal structurally weak and less safe.
Pin On Projekty Do Wyprobowania
How To Shape Fenders Sheet Metal Fabrication Metal Shaping Metal Fabrication
Pull Dents With The Help Of Your Mig Welder With The Eastwood Mig Stud Welding Kit Auto Body Shop Auto Body Repair Metal Working Projects
How To Weld Sheet Metal On A Car Handyman Tips Welding And Fabrication Diy Welding Sheet Metal
How To Make Your Own Car Body Repair Panels Hammer Forming Tips And Tric Auto Body Repair Auto Body Work Auto Body
Pin By Jeff Hoffman On Fabrication Sheet Metal Work Custom Metal Fabrication Auto Body Work
Metal Fabrication Metal Shaping Custom Car Parts Metal Fabrication
0 comments:
Post a Comment