Failure of a welded joint can be of two types. Fatigue is the phenomenon that occurs in bolt materials as the result of cyclic variations of the applied stress.
Liquid Zinc Penetration Induced Intergranular Brittle Cracking In Resistance Spot Welding Of Galvannealed Advanced High Strength Steel Springerlink
3 The maximum shear stress due to bending is determined.
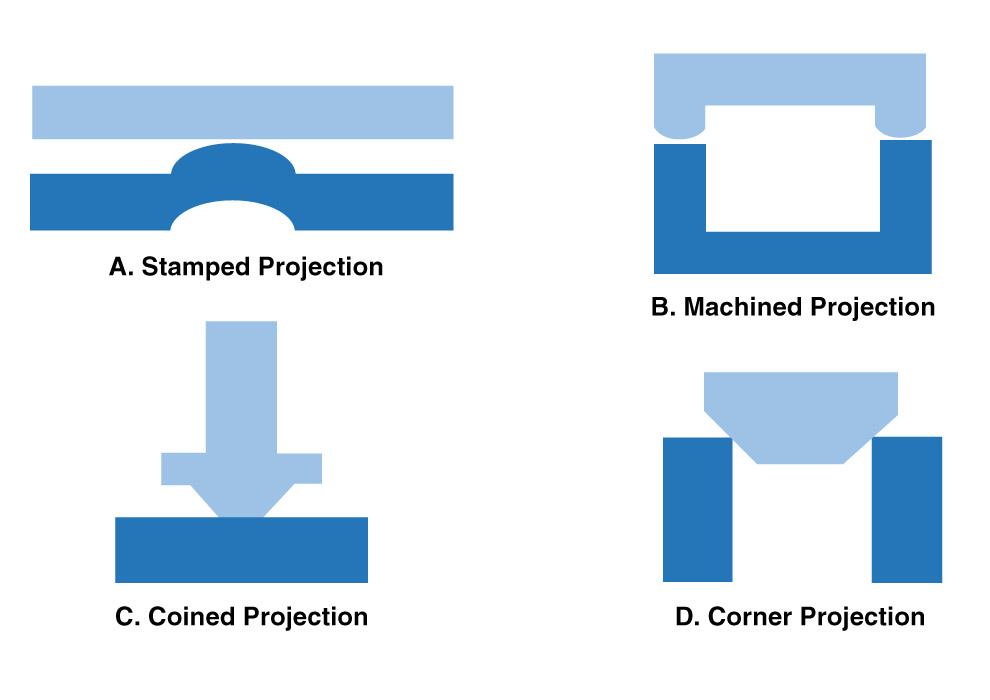
Projection welding failure modes. τ b MyI u. Failure Modes and Effects Analysis FMEA of Welded. In the case of two dissimilar thicknesses t.
Failures and their causes. Projection Welding Projection welding is a resistance welding process wherein coalescence is produced by the heat obtained from resistance to electric flow through the work parts held together under pressure by predetermined points by projections embossments or intersections. Ton pull fracture partial thickness fracture and interfacial fracture are the three failure modes of nut projec-tion welded joints.
Failure mode effect analysis FMEA was done to determine the risk priority number RPN against each cause and factor with higher RPN was selected for improvement. 1 The area of the fillet weld A uunit thickness is calculated assuming the weld is one unit thick. While pub lished resistance spot welding schedules assume that welds are made without expulsion this seldom occurs in produc tion where a high percentage of spot welds are actually made with expulsion.
Z Development of Recommended Actions is targeted at eliminating the Root Cause of the potential failures. Other less likely modes include a gross corrosion defect and the rupture of a part-depth or through-wall crack. One of the most common failure mechanisms for bolts is fatigue.
Tice is considered to be one that operates just below initial expulsion. When welded with projection welding most of the zinc plating gets flashed out during the early part of the weld cycle. Also the preparation of the weld joint.
Main drive is to understand the process through the identification of as many potential failuresas possible. The most likely mode of canister confinement failure is the through-wall growth and vi penetration of a crack. And weak strength of the welded joint.
Consider the age and cleanliness of the wire and parent material. Electrical short-circuiting corrosion or deformationA failure mode in one component can lead to a failure mode in another component therefore each failure mode should be listed in technical terms and. Weld fails in the pullout mode.
Welding Research Armco Inc Research Technology Middletown Ohio. The results when welding tin-plated copper parts are similar. The plating should have a lower melting point than the base alloy.
To develop the failure criterion of spot welds we first per-formed the strength test using cross tension and lap-shear or. The interfacial fracture is brittle rupture and the partial thickness fracture is ductile rupture. 2 The unit Moment of Inertia I u is calculated assuming the weld is one unit thick.
A those failed during inspection. The failure mode and effect analysis tool plays a key role for the improvement in the production rate and reduced in the failure. Classification of welding processes 150 100 50-100-150.
Projection Plasma Gas Metal Arc Fig. Other things to consider are the type of wire Is it compatable with the grade of aluminium the wire thickness the weld settings current voltage pulsed or non pulsed the torch position and angle to the weld. The objective of this study is to develop an engineering failure criterion for spot weld in thin sheet metals under nugget pullout mode.
Incorrect material used z PFMEA typically assumes that the design is sound. Failure of spot weld under impact loading as well as fatigue loading will be the subject of future reports from our investigation. INTRODUCTION A projection welding is a resistance welding where high electrical resistance at the joint is developed by embossing.
Tin plating is squeezed out and allows base copper on both sides to come in contact and form a strong copper-copper solid-state bond see Figure 5. Region are again more important because the two modes of failures eg fatigue. Buttibori Nagpuron welding processto reduced the failure in the base frame.
In this project the Failure Mode and Effect Analysis is implemented in LEMKEN INDIA AGRO EQUPMENT PVT. 1 Lower limit This equates to the welding conditions which result in a weld diameter equal to 35 t where t equal sheet thickness in mm.
Pdf Application Of Failure Modes And Effects Analysis Fmea In Automated Spot Welding Process Of An Automobile Industry A Case Study
Https Www Mdpi Com 2075 4701 10 10 1279 Pdf
Pdf Effect Of Weld Nugget Size On Overload Failure Mode Of Resistance Spot Welds
Resistance Spot Weld Failure Mode And Weld Performance For Aluminum Alloys Sciencedirect
Resistance Spot Weld Failure Mode And Weld Performance For Aluminum Alloys Sciencedirect
Https Www Mdpi Com 2075 4701 8 10 764 Pdf
0 comments:
Post a Comment