But as it heats up you back off to much less than that. This is why it is common for TIG aluminum to warp where a MIG process on the same application does not warp as bad.
Tig Welding Thin Aluminum How To Make Tig Welding Filler Rod How To Tig Weld Aluminum Youtube
The aluminum oxide layer must be removed using a stainless-steel wire brush and acetone.
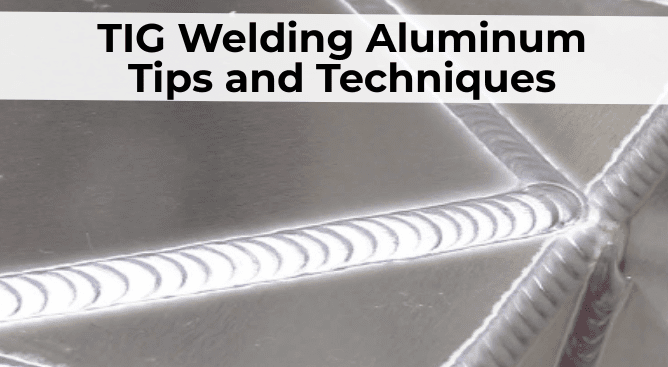
How to tig weld aluminum without warping. Many sources say a TIG welder is the best method for welding aluminum. You can accomplish this by using a skip welding technique. To minimize warping distribute heat as evenly as possible.
Our copper weld backers help to keep a welds from blowing through the metal and also act as a heat sink. With a little bit of practice you will be able to generate decent welding results even if you are just a beginner in the field. Use a stainless steel wire brush used exclusively for aluminum to remove surface oxides.
We cover basics for beginners who want to TIG wel. To prevent warping it is important to get the the pieces clamped into position and make many many tacks. Another alternative is to surround the area youre welding with an Anti-Heat Compound that will block the heat from spreading to the rest of the panel and potentially reduce warping in the panel.
The process requires joints with no gaps. Skipping this step often results in wasting good aluminum. Unevenly distributed heat causes distortion and warping which wreaks havoc on parts that should fit together.
Welding on both sides of the plate offsets one shrinkage force with another to minimize warpage Figure 4. Keep the torch in a steady forward-moving position with a slight backward tilt of 5 to 15 degrees. The aluminum of that size should be very easy to weld with almost no distortion but the nature of metal fab is that sometime parts do warp.
Use a solvent such as acetone or a mild alkaline solution like a strong soap to remove any oil grease and water vapor from the aluminums surface. This can also be done with a strong alkaline or acid. There is a rule of thumb that one amp per one thousandths of thickness up to around 125 will get you pretty close.
You can fit it in a hole and weld around or just butt it against the angle and fillet weld which is stronger. It could be mig welded also. Hold the torch by bracing it with the base of your hand from your wrist to the tip or your pinky finger flat against the table.
Balance welds around the neutral axis. Long story short the sides have to be welded together to make a full. I am in the process of building an enclosure for a research vessels J-frame controls.
TIG Welding can be used to weld aluminium copper titanium etc and even two dissimilar metals. The pieces should be tacked in 3 or 4 places and then welded in one continuous direction around the tube. TIG welding is quite an easy process once you get a hold of it.
Most common is the intial puddle initiation. Learn how to TIG Weld. Here is a list of the equipment that you need.
But 15 amps per thousandths along with a. Then midway between those tacks and then midway between those tacks and so on. Well for aluminum you might need as much as 15 amps per thou.
Long time lurker first time poster. Place welds near the neutral axis or the center of the part. How to TIG weld aluminum without filler rod.
Reduce warpage by providing less leverage for the shrinkage forces to pull the plates out of alignment. This video is sponsored by LincolnElectric to demonstrate the TIG 200 Square Wave. This process is ideally suited to handling tricky welds such as S-Shapes curves corners or where the weld is going to be visible and where accuracy and finish is important.
Here are some helpful tig welding aluminum tips to help you learn how to weld aluminum faster than you would have otherwise. Id start by dividing the seam length into thirds and take near middle and far. The keys to TIG welding aluminum without filler rod are in the cleaning of the material and the fitting of the joints.
Sitting there waitng for the puddle to form is the kiss of death for warpage control. Cleaning the aluminum surface before starting your TIG weld can be done in two vital steps such as. This process involves getting two pieces of aluminum to stick together without breaking shriveling warping or cracking.
Tig is the way to go. Materials that are thicker than 18 work best. Wanted to build with sides made of full sheets of 14 6061 aluminum but the engineer had other plans.
This is especially helpful if youre welding in an area that is very critical and could lead to oil canning. Eliminate the contaminants and oils from the aluminum surface. Here are some techniques that you should follow while performing DC-TIG aluminum welding.
Preheating alum is a good thing but with the thicknesses you have not really necessary. You must floor the current control establish your puddle immediatly.
Tig Welding How To Tig Weld Process Overview And Machine Setup Gowelding Org
Tig Welding How To Tig Weld Process Overview And Machine Setup Gowelding Org
Bangshift Com Here S How To Tig Weld Aluminum Tanks Make Your Own At Home Bangshift Com
Inno Aluminium Tig Welding Services Posts Facebook
Tig Welding Aluminum Tips And Techniques
Tig Aluminum What Causes It To Do This Welding
How To Tig Weld Steel And Aluminum Basics Setup And Tips
Getting Started With Tig Welding Plasmargon
0 comments:
Post a Comment