Testing of welds is used to verify that the welding procedure is under control. Part 1 Arc and gas welding of steels and arc welding of nickel and nickel alloys.
Metals Free Full Text Comparison Of Finite Element Methods In Fusion Welding Processes A Review Html
ME0860 is serial numberspecific to identify the date and place of manufacture and represent the condition of Miller products as delivered from the factory.
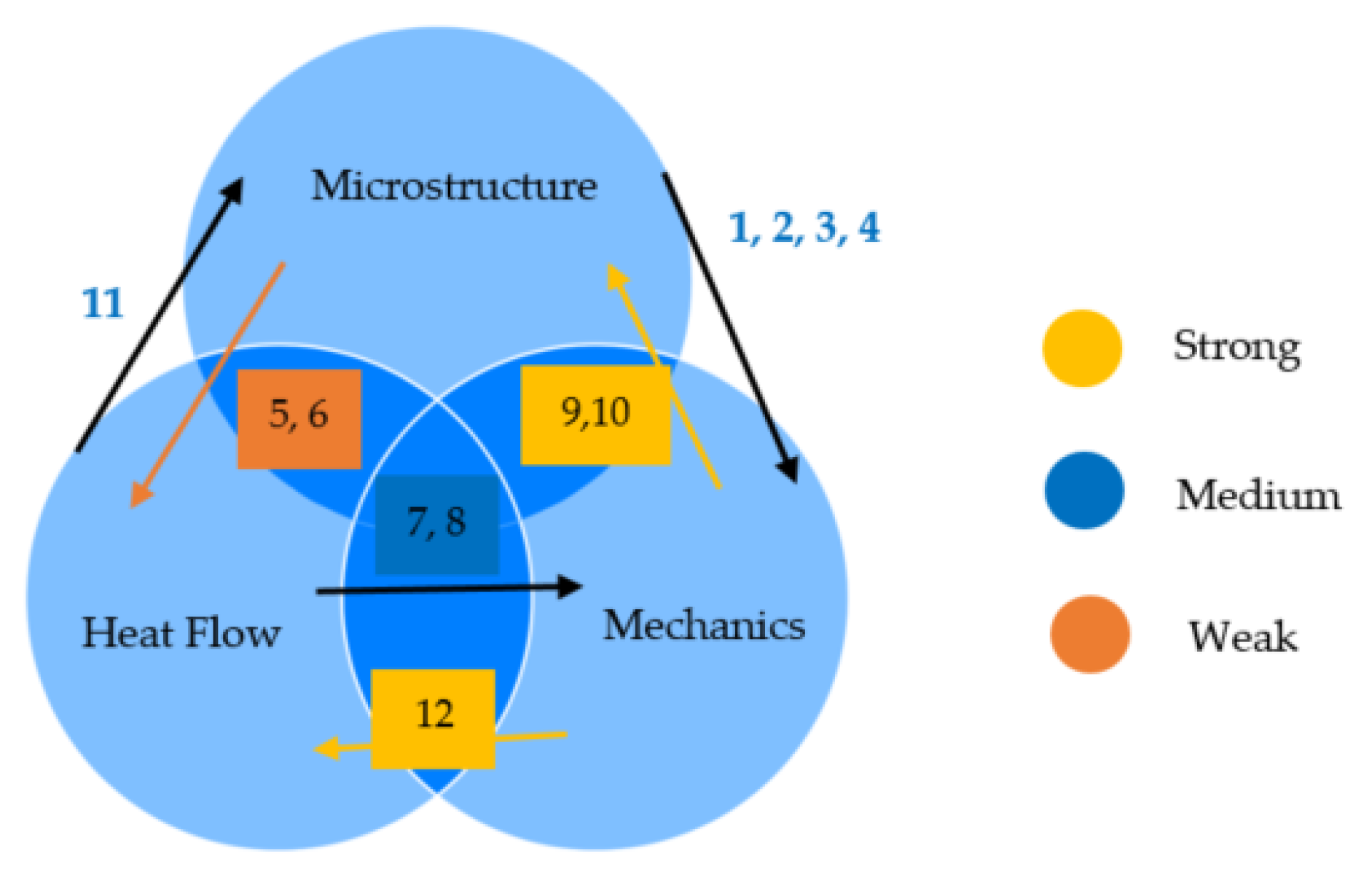
How to validate welding process. Process Validation Plan Template. Welding-validation of parameters is used to describe the assessment of a Welding Procedure Specification WPS generally in an experimental situation as opposed to a production environment. Make a qualification weld 4.
To what accuracy the equipment is to be validated. Certification The process of performing calibration andor validation tests per applicable Standards and formally documenting the results. 2 The operators must be trained and skilled to do the job.
What occurs during IQ OQ PQ. Fusion and pressure welding of non-alloyed and low-alloyed cast irons. The WeldScanner Validator is delivered as a calibrated system and should be calibrated on an annual basis eg.
Process Validation Sop Template. An Article titled Validating the Resistance Welding Process was published in the December 2009 Issue of the Welding Journal at page 42. 3 The destructive testing must be carried out as per defined frequencycustomer rqmnt.
Process Validation Protocol Template. Temperature pressure colling water temp etc. Process Validation Template Pdf.
Only qualified personnel may validate a process. Dies transferred or new are inspected and compared to print. A Tip and b Shaft.
Establish the initial validation of welding equipment. Both parts are made from 304L stainless. All activities which have been carried out must be recorded including date and signature.
Accuracy of welding equipment Validation is the procedure of demonstrating that the equipment conforms to the operating specification. In our laboratory to ensure compliance with the standards also providing traceability to national standards. 24 posts related to Welding Process Validation Template.
Laser Welding Validation Example While this article uses a minimally invasive surgical tool to illustrate the laser welding validation process this basic validation process applies to all laser welding applications. Understand the intended application for which the WPS will be used 2. The surgical tool shown in Figure-2 consists of two parts.
To pass the test the surgical tool could not exhibit any leaks when subjected to pressure of 689 MPa over a 20-sec period. If the fixtures are commissioned on the manufacturing floor and dont produce good parts consistently and efficiently then the return on investment ROI for the weld tooling is greatly reduced. July 5 2020 by Mathilde Émond.
Specification and qualification of welding procedures for metallic materials - Welding Procedure test. Weld fixture validation and run-off is obviously a critical step in the fixture building process. Must be as per defined standards.
Therefore before validation can be carried out it is necessary to establish the specification ie. The first test used to achieve a process validation weld-quality metric was a leak test based on helium gas. WELDING PROCEDURE PREPARATION.
Arc welding of aluminium and its alloys. Welding Process Validation Template. Requirements to calibrate verify and validate as part of inspection testing non-destructive testing or measuring of final welded products performed in order to verify confirm product compliance are outside the scope of the present International Standard.
Fillet The box marked fillet should be checked if the weld is a weld of approximately triangular cross section joining two surfaces approximately at right angles to each other in a lap-joint T-joint or corner joint. Tests involved in Welding Process Validation - Non-destructive NDT Test Visual Test VT - Visual appreance and size of welds to be determined Ultrasonic Test UT - Soundness of the welding to be determined. Weld testing even if not required by specifications helps welders to check and improve their own technique.
It is made on test pieces intended for destructive testing. A successful validation process can also lead to improved productivity reduced risk of recall and a less burdensome process for investigating consumer complaints. Among the test are tension and bend tests made on specimens of a certain shape.
The device ensures precise measurement for welding voltage welding current wire feed speed and optional the gas flow rate and travel speed. Welding-testing is used to determine the soundness of welds. Five Step Process to Qualify a Welding Procedure 1.
These validation activities must comprise. Develop a draft procedure 3. Procedures with which process parameters are surveilled must be established.
As welding is considered as special processso it needs validation such as 1 Welding parameters. Verify that these requirements are met. Process validation involves correlating process qualification data with process validation data.
Process validation is only required if process outcomes cannot be verified.
Fda Software Validation 2020 Guide Checklist Template
Macroscopic Cross Section Of A Weld Seam Produced By Gas Metal Arc Welding Download Scientific Diagram
Metals Free Full Text Comparison Of Finite Element Methods In Fusion Welding Processes A Review Html
Steering A Battery Manufacturer S Application Through The U S Fda Validation Process Electronic Products
How To Solve Common Ultrasonic Welding Problems Plastics Technology
The Role Of Process Characterization In Process Validation
Flow Chart Of The Welding Simulation Procedure Download Scientific Diagram
Example Welding Parameters With The Cmt Process Download Table
0 comments:
Post a Comment