GOOD WELD QUALITY IS. No cracks or holes found in the bead.
Mig Vs Tig Welding Types Materials And Applications A Guide
Since then it has become possible to manage the quality of welding based on the work standard specifying the materials and instruments to be used and the.
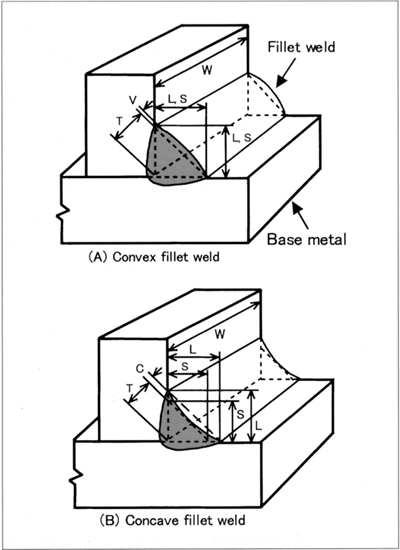
Welding quality meaning. Now lets see the different types and their examples. Welding Quality - ISO 9001 ISO 3834 Quality Requirements. It is used to prepare joints for connection in the shop and on site and for the attachment of other fixtures and fittings.
The stressless recrystallization zone consists of crystals with a spherulitic shape indicating that crystallization occurred under no significant stress. This means that you cannot make a complete verification of the welded joint without destroying it and that it requires Specialist management. Width of weld is equal through out its length.
All welding is carried out on the welders own risk and account. Description of the quality of a weld on the basis of type size and amount of selected imperfections Imperfection. There are a lot of ways to make this weld and they mostly have differences based on geometry and edge preparation.
The product meets the required design dimensions has almost no distortion and is finished accurately with its appearance satisfying the required level. The Welder Qualification needs to be performed to confirm the welders ability to deposit sound weld metal for a specific type of weld material and weld position. The product meets the.
Welding is an integral part of the manufacturing process of steel fabrications and is identified as a special process that requires special control measures to be implemented to ensure weld quality. Welding is a core activity in the fabrication factory undertaken by skilled qualified operatives working to a welding quality management system under the control of a Responsible Welding Coordinator. Weld is free from any type of defect.
We say that the welding quality is good if it suffices the following requirements. This is because it was difficult to check the quality requirements at that time. Welding should be executed by a qualified and experienced Welding should be executed by a qualified and experienced welder and adequate safety measures should always be adhered to.
The martensitic grades produce poorer quality welds then the austenitic and ferritic grades. The HAZ consists of three zones in addition to the weld flash. Uniform filling of the weld.
Is this an acceptable quality standard. The inspector does this by performing visual inspections on the welded steel pieces as well as testing them for possible defects. In the first edition of ISO 9000 1987 welding was defined as a special process.
The high carbon levels Table 46 produce very hard and brittle HAZs and welds due to the formation of martensiteIf carbon contents above 01 have to be welded then an austenitic stainless steel filler material should be used to improve weld toughness and to avoid weld cracking. Moreover MIG welds are great if not perfect. Knowing how to do this well and how to read its symbols is paramount to being a quality welder.
Square groove weld means that you wont be beveling the. The basic conditions of welding quality to achieve products of such high quality includes the following. Fusion weldingdiscontinuity in the weld or a deviation from the intended geometry.
Welding is considered as a Special Process which means that its quality cannot be readily verified and its successful application requires specialist management personnel and procedures above and beyond those that are considered for general quality systems such as ISO 9001. The bead has uniform waves width and height. The Welder Qualification is valid for a range of materials thicknesses positions and types of welds depending on the qualification standard.
One of the major reasons why MIG welding is so common is that it can be used to weld any metal almost. Weld quality is determined by the microstructure of the HAZ of the weld. The welding meets the required strength.
Welding Quality Assurance Inspectors are needed to inspect welds 1 to be sure they have been performed according to contract requirements and are up to the specific state codes and standards in the industry. The weld quality is directly related to weld design magnitude of residual stresses strain set up by welding heat layout of welded joint quality of base metal and quality of work preparation and fit ups. Welding quality and problems.
Although the weld quality from MIG welding is not superior to other types of welding MIG welding is one of the fastest and the most cost-efficient welding processes. We visited a customer yesterday that said their quality standard for welding is simply no porosity and no lack of fusion This is tough since visual inspection cant detect lack of fusion and they are not doing any other kind of nondestructive testing. The finished product satisfies the design dimensions and has almost no distortion.
Chapter 12 Flux Cored Arc Welding Equipment Setup
Wqcp Welding Quality Control Plan By Acronymsandslang Com
The Abc S Of Arc Welding Education Center Kobelco Kobe Steel Ltd
Types Of Welding Joints The 5 Different Types Of Welding Joints
Weld Defects Weld Discontinuities Distortion And Its Controls Ppt Video Online Download
Tig Welding Or Gas Tungsten Arc Welding Gtaw Process
Difference Between Smaw Gmaw And Gtaw Welding Processes
Mig Vs Tig Welding Types Materials And Applications A Guide
0 comments:
Post a Comment