In order to highlight the importance of contact resistance we consider two electrically conductive bod-ies which are in contact under an applied force F see Fig. Spot welding is a resistance welding process for joining metal sheets by directly applying opposing forces with electrodes with pointed tips.
Weldability And Shear Strength Feasibility Study For Automotive Electric Vehicle Battery Tab Interconnects Springerlink
As different welding position sequences for three.
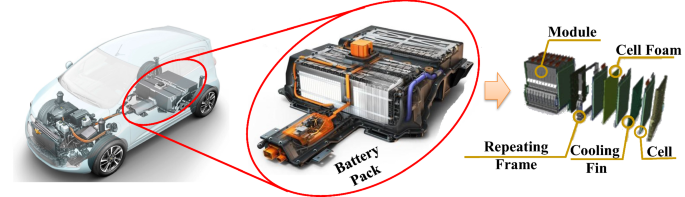
Welding techniques for battery cells and resulting electrical contact resistance. A higher electrode force will reduce contact resistance which in turn will reduce heat at the contact points electrode-to-part and part-to-part interfaces. Although soldering techniques have some significant advantages welding techniques such as spot and laser welding are mostly used within the industrial production of batteries. This technique works because the heat generated in the work piece is distributed based on where the electrical resistance is.
The resistance spot ultrasonic laser welding micro friction stir blind riveting FSBR micro friction stir forming FSF and micro friction stir welding FSW are the common joining techniques. The results presented in this paper show that laser beam welding with continuous wave radiation is a suitable joining process for the electrical connection of 26650 battery cells while avoiding a critical temperature change within the cells. The weld nugget size is usually defined by the electrode tip contact.
A wide spectrum of welding applications including prismatic and cylindrical Li-ion batteries by utilizing longitudinal or torsional welding techniques. Resistance spot welding RSW works on the principle of electrical resistance at the mating surfaces when high current passes through them creating localised heating and fusion of materials under pressure. Resistance spot ultrasonic or laser beam welding are mostly used for connecting battery cells in the production of large battery assemblies.
Round cell is done with Telsonic Ultrasonics using the longitudinal or alternatively the torsional welding. Resistance spot ultrasonic or laser beam welding are mostly used for connecting battery cells in the production of large battery assemblies. Owing to the sur-.
Cell casing and terminal dimensions may constrain possible contact geometries. The compared techniques are resistance spot welding laser beam welding and ultrasonic welding. Welding techniques for welding batteries.
Contact resistance is an important factor in the first few milliseconds of a weldCombined with bulk resistance the contact resistance value of the workpieces electrodes and their interfaces both cause and affect the amount of heat generated. The contact between the tab and the inner cell casing must be mechanically strong and have low electrical contact resistance. Each of these welding techniques has its own characteristics depending on the material properties and contact geometry.
Laser welding with high power fiber laser systems can produce complete battery modules that reach the capacities and cell voltages eg 400 V or 800 V required for electrical vehicles 3. Finally the suistriple welding parameter setting ranges were obtained as. Cell casing and terminal dimensions may constrain possible contact geometries.
The electric resistance and mechanical strength of the welded contact were measured. All three methods are tried and proven to function in the production of battery applications. Each of these welding techniques has its own characteristics depending on the material properties and contact geometry.
Lap shear and T-peel tests are performed to evaluate the joint strength. In common battery assemblies the joint between the battery cell and the current collector cell connector is realized by different welding techniques like spot laser beam or ultrasonic welding. For example pouch cells provide detached tabs whereas cells.
The joining techniques with application for battery tab interconnects are ultrasonic metal welding resistance spot welding and pulsed TIG spot welding. An alternative joint for connecting battery cells is a clamped electrical contact. The performance was evaluated in terms of numerous factors such as production cost degree of automation and weld quality.
In the penultimate section of this work soldering is compared to welding techniques and press contacts in terms of electrical connection resistances and ultimate tensile force. 1b surfaces irregularities are schematically shown in a magnified portion of the contact interface. Electrical joints with a low contact resistance and a high mechanical strength can be achieved.
The current and the heat generation are localized by the form of the electrodes. The weld quality of the joint is an important factor in determining the performance and safety of the battery. In resistance welding contact resistance is a function of the extent to which two surfaces come in contact.
To weld different positions it results in structural deformation of the positive battery terminal which directly affects the contact pressure. In the cell assembly the bonding of the conductor foils anode - copper and cathode - aluminium with the cell conductors pouch cell or with the contact terminals eg.
Weldability And Shear Strength Feasibility Study For Automotive Electric Vehicle Battery Tab Interconnects Springerlink
Weldability And Shear Strength Feasibility Study For Automotive Electric Vehicle Battery Tab Interconnects Springerlink
Weldability And Shear Strength Feasibility Study For Automotive Electric Vehicle Battery Tab Interconnects Springerlink
Overlap Joining Of Aluminium And Copper Using Laser Micro Welding With Spatial Power Modulation Springerlink
Weldability And Shear Strength Feasibility Study For Automotive Electric Vehicle Battery Tab Interconnects Springerlink
Pdf Expulsion Reduction In Resistance Spot Welding By Controlling Of Welding Current Waveform
Overlap Joining Of Aluminium And Copper Using Laser Micro Welding With Spatial Power Modulation Springerlink
Overlap Joining Of Aluminium And Copper Using Laser Micro Welding With Spatial Power Modulation Springerlink
Weldability And Shear Strength Feasibility Study For Automotive Electric Vehicle Battery Tab Interconnects Springerlink
0 comments:
Post a Comment