How to Weld Thick to Thin Aluminum with Super Alloy 5 Aluminum Rod and Flux Repair Kit - YouTube. If the aluminum is located near a heat sensitive surface we recommend pairing Super Alloy 5 with Heat Freeze Heat Paste.
Aluminum Gas Welding The Basics Weld Guru
On the other hand a 5-inch thick sheet must be preheated at about 400 degrees Celcius.
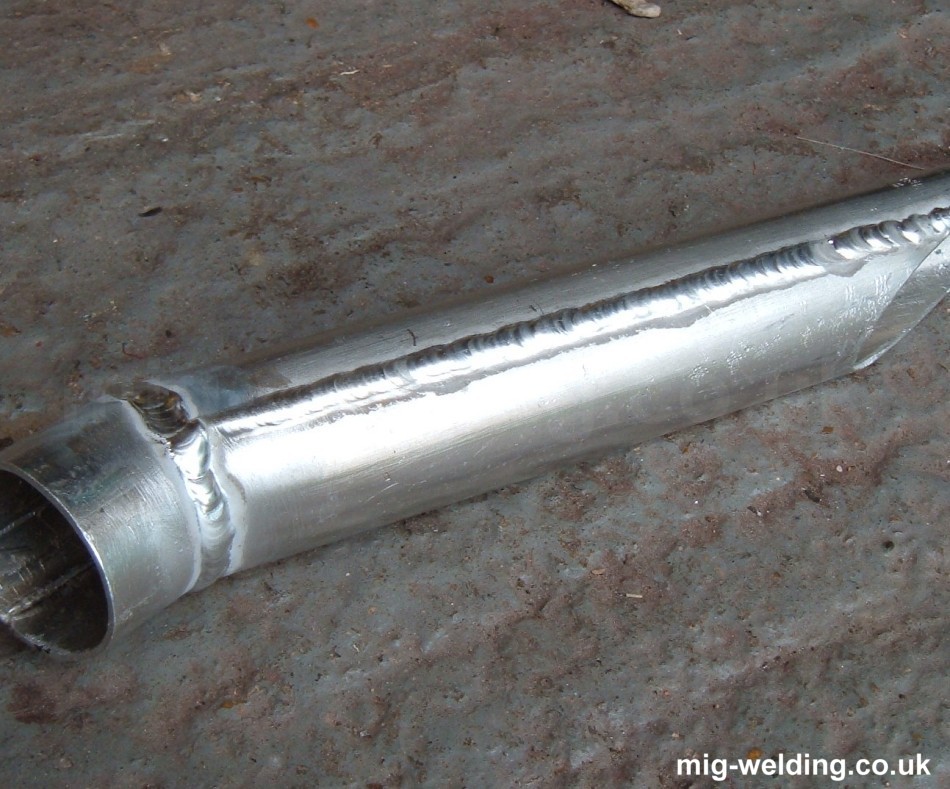
How to weld thin alloy. But 15 amps per thousandths along with a. Welding of High Alloy Materials. Thin aluminum is repaired easily with propane or mapp gas thick aluminum requires an oxyacetylene torch.
For example an inch thick sheet of copper must be heated at 60 degrees Celcius. The connection between the thin tube and the thin tube may be in the form of curling flanging using argon arc self-fusion or suitable wire bonding. Please observe all AWS Safety Health Guidelines when using Muggy Weld products.
When a welder uses tig welding in thick copper he must preheat the copper alloy up to 350 degrees Celcius. This material and its alloys are readily fusion welded providing suitable precautions are taken. TIG and plasma processes with argon or argon-helium shielding gas are used for welding thin section components typically.
This method is not limited to them since it is used on other materials such as copper alloys magnesium and aluminum. To the weld face risk the possibility of insufficient alloying in the weld root. However if the base metal is cold 12C or less it should be warmed to at least 20C above the ambient temperature to prevent I the formation of condensate as moisture can cause weld porosity.
Typically Alloy C-22 13 Mo is used. When welding in narrow groove joints uses an electrode small enough to properly reach the bottom of the joint. It will transform into a liquid when the thick piece has been heated to working temperature.
Pulse TIG welding is usually used to weld thin sections of the stainless steel material and non-ferrous metals. If Alloy C-22 is not available Alloy 625 9 Mo or Alloy C-276 15 Mo may be substituted. How to MIG Weld Aluminium Strike a clean welding electrode around an inch from the start of your weld then quickly move it over to the point where you want to start welding.
Super Alloy 5 polishes beautifully and will hold a polish as long as the parent aluminum. The torch and electrode. Zinc rods that have no flux do not polish or hold a polish.
Autogenous welding can be used for a section thickness of. As we weld we just kiss the edge of the thinner part and focus the majority of the heat towards the thicker part. .
Preheating nickel alloys prior to welding is not normally required. The more weld passes a welder makes the greater the chance of shrinking the materials. Possible methods of welding magnesium alloys include.
The welding assembly method is like this. A welder should weld from left to right placing every weld seam from left to right rather than the opposite way. The composition of the parent metal should be known before welding any alloy elements present will absorb into the weld also the use of several weld passes will assist in making welds less brittle.
Well for aluminum you might need as much as 15 amps per thou. Another technique we can use is to set the amperage just high enough to weld the thicker of the two metal parts. Amperage of TIG Welding on Steel.
You should weld near the neutral axis or the center or the part. The thin tube is welded to the thick tube and is usually welded by a plug-in method. Apply the flux to the joint using the aluminum welding rod and continue to apply heat to the thick piece of aluminum.
X Spot welding x Arc welding x Friction stir welding x Laser welding The first two methods are suitable for joining th ick plates but not very thin sheets because of the high heat input. There is a rule of thumb that one amp per one thousandths of thickness up to around 125 will get you pretty close. But as it heats up you back off to much less than that.
The alloy of the insert ring must have a higher molybdenum content than the AL-6XN to compensate for alloy dilution on cooling. Use a string bead technique as you move along the weld but be careful not to.
How To Weld Aluminum Australian General Engineering Vietnam Metal Fabrication Vietnam
How To Weld Aluminum Australian General Engineering Vietnam Metal Fabrication Vietnam
Aluminum Welding Guide Tips Techniques Weld Guru
Tig Welding Thin Aluminum Youtube
Welding Stainless Steel To Aluminum Welding Tig Time Youtube
How To Weld Aluminum Australian General Engineering Vietnam Metal Fabrication Vietnam
How To Weld Aluminum For Beginners Youtube
0 comments:
Post a Comment